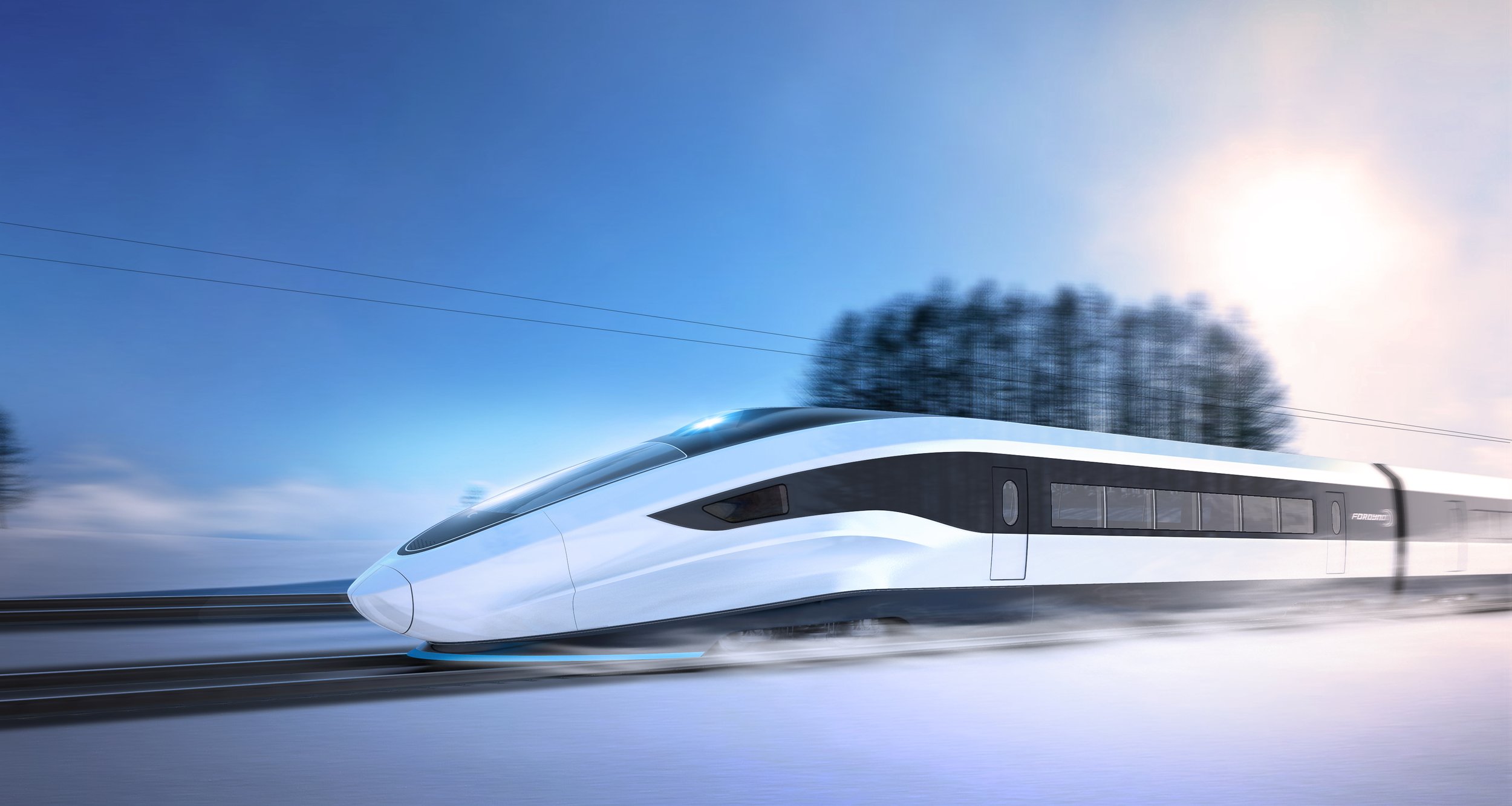
Industrial Design.
Strategy and innovation starts with a thorough understanding of what your product could be, what it needs to do, and where in the market it will have the most impact.
Our design team utilises market research and insights to develop coherent, beautiful and functional products, that maximise your impact on the market.
We continue to work with innovative brands to ensure consistent brand and product experiences at every touchpoint, supporting growth and market maturity over time.
-
Market research.
Ethnographic research.
Innovation roadmap.
Brand positioning.
Portfolio architecture.
-
Concept design generation.
CAD development and surfacing.
CMF development.
Ergonomics and human factors.
Design visualisation and CGI.
-
Brand design and development.
Launch strategies and implementation.
Marketing collateral, CGI imagery, animation and VR experiences.
Engineering.
Fordyno utilises our inhouse expertise to design complex structures manufactured from metal or composite materials.
Our team apply their extensive experience to ensure that parts are easy to manufacture while meeting structural requirements such as fatigue, mass, strength and stiffness.
Our engineering team have extensive experience bringing designs to production with many projects now in service with our clients and their customers.
-
Structural engineering.
FEA simulation and analysis.
Crashworthiness modelling.
Production support,
-
Research and development into new materials and methods of production.
Interfacing with existing surfaces from 3D scan data.
Lightweight design.
Cost optimisation.
-
Project planning and program development.
Project budgeting.
Feasability analysis.
Bid submission writing.
Technical compliance reviews.
Localisation planning.
Manufacturing.
Fordyno's additive manufacturing capabilities allows us to provide fast prototyping, rapid development and modification of components, and parts made with unique geometry that is not feasible with other manufacturing methods.
Our engineering team has linked our FE analysis software with the 3D print path for continuous fibre-reinforced components allowing us to analyse, optimise, and certify component design for safety critical applications in transport, mining or other industries. With continuous monitoring during manufacture, we have automated quality assurance for your 3D printed parts.
Applying our Design for Additive Manufacturing expertise, we optimise material use reducing costs, print time and component weight. With expertise in bonding, we can also produce parts that are larger than the machine constraints.
Our equipment can produce parts from metals, plastics and continuous fibre-reinforced plastic to best suit your application.
-
Validation of 3D printed components.
Bonded parts for larger components.
-
Low volume production for testing and development.
-
Repeatability.
Continuous monitoring and improvement of mass produced parts.
Automated quality assurance.